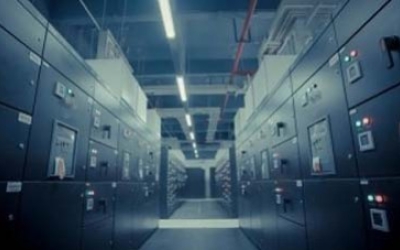
Design and manufacture of leakproof and waterproof electrical enclosures
Share this content
In industries where explosive atmospheres are present, explosion-proof electrical boxes become crucial. This article explores in depth the principles behind their design, from ATEX regulations to rigorous manufacturing techniques, and the judicious choice of explosion-resistant materials.
In high-risk industrial environments, protection against explosions and dust or water infiltration is essential to ensure the safety and proper functioning of electrical equipment. Fold-proof and waterproof electrical boxes play a crucial role in these contexts. This article explores the design and manufacturing principles of these boxes, highlighting safety standards, materials used and manufacturing steps.
The anti-explosive electrical enclosures are designed to contain any explosion that may occur inside the enclosure, preventing its spread outside. They are essential in industries where explosive atmospheres can be present, such as the petrochemical, mining and manufacturing industries. In parallel, waterproof housings protect electrical equipment against moisture, dust and other environmental contaminants, thus ensuring their optimal functioning and longevity.
ATEX standards
Anti-explosive containers must comply with ATEX (Explosible Atmospheres) guidelines in Europe, which define requirements for equipment used in potentially explosive environments. Key standards include:
Directive 2014/34/EU (ATEX 114): Concerning protective equipment and systems intended for use in explosive atmospheres.
Directive 1999/92/EC (ATEX 153): Concerning the protection of workers who may be exposed to the risks of explosive atmospheres.
IEECx standards
At the international level, the International Electrotechnical Commission System for Certification to Standards relating to Equipment for use in Explosive Atmospheres (IECEx) standards regulate the certification of equipment for explosive atmospheres, ensuring a safety equivalent to that of ATEX standards.
The selection of materials for blast-proof and waterproof housings is crucial to ensure their efficiency and durability. Commonly used materials include:
Stainless steel : Provides exceptional corrosion resistance and high strength, suitable for aggressive environments.
Aluminium: Lightweight, corrosion resistant and easy to manufacture, it is often used for cases requiring good thermal conductivity.
Glass fibre reinforced polyester: Resistant to shocks, corrosion and UV rays, it is ideal for outdoor and marine environments.
Sealing of the enclosures is ensured by seals made of resistant materials such as silicone or elastomer. These seals are placed on the edges of doors and panels to prevent dust, water and other contaminants from entering.
The blast-proof enclosures shall be designed to withstand internal pressure caused by an explosion. Design features include:
Manufacturing Steps
Design and Prototyping: Engineers design boxes using CAD software, followed by prototypes for testing.
Selection of Materials: Choice of materials based on strength, durability and compliance requirements.
Manufacturing: Cutting, forming and assembly of components using welding, moulding or machining techniques.
Application of the Joints: Installation of seals to ensure protection against intrusions.
Compliance Tests: Strict tests to ensure that enclosures meet ATEX and IECEx standards, including tests for pressure, watertightness and corrosion resistance.
Quality Control: Each stage of manufacturing is subject to strict quality controls to ensure that the boxes meet safety specifications and standards. The final tests include checks on mechanical strength, tightness and overall performance in real-life conditions.
The design and manufacturing of exhaust-proof and watertight electrical boxesare complex processes requiring in-depth technical expertise and knowledge of safety standards. By selecting the right materials and following rigorous manufacturing practices, manufacturers can produce boxes that ensure optimal protection in the most demanding environments. Compliance with ATEX and IECEx standards is essential to ensure the safety of people and equipment, while ensuring reliable and sustainable performance of industrial electrical installations.
Share this content
check_circle
check_circle
Nous utilisons des cookies tiers pour améliorer votre expérience de navigation, analyser le trafic du site et personnaliser le contenu et les publicités. En savoir plus